Whether your pump is responsible for moving raw materials out of your storage tank to the core reactor or thick slurries back out to the wastewater treatment area, you rely on pumps to keep production moving.
Installing a new pump can throw a wrench in your gears, but the pros of a new pump often far outweigh the cons. To avoid significant downtime during installation, there are some things you can do to prepare before working with a professional installation team.
Our team has successfully managed thousands of pump installations and start-ups. In this blog, we will break down eight tips that help expedite the process and ensure a successful installation and start-up.
1. Work Permits
Before you start the job and when applicable, ensure that you have the correct work permits for the process area where the installation will take place. Work permits grant you the appropriate access before entering a production or process area. They describe the hazards in the area where you will be working and ways to mitigate them. An approved work permit alerts the rest of the facility that work is about to begin in a particular area.
2. LOTO
Pumps store a lot of energy that can quickly dissipate if not managed correctly. Ensure that you have performed a robust Lock Out Tag Out (LOTO) procedure before beginning installation. This way, you will be able to isolate any process material from the installation area. You don’t want your product leaking out of a pipe connection before you even get started.
3. Electrical Isolation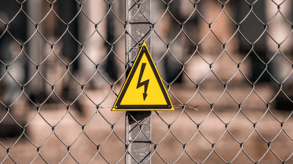
You also need to address any electrical hazards when it comes to pump installation. Properly isolate the area from all electrical sources prior to installation to avoid the risk of an electrical shock. Additionally, you should work with a certified pump installation expert to safely disconnect and isolate all electrical connections.
4. VFD Setup
Many pumps can only be operated at one speed with a set flow rate. Certain Discflo pumps, however, are driven by a Variable Frequency Drive (VFD) that allows you to operate at a range of speeds and flow rates. Using a VFD gives you greater control and flexibility in managing your pump operations. Ensure that you work closely with your pump installation expert to set up the VFD correctly. If not, you risk the pump not running properly following installation.
5. Air Vents
In certain applications, air and other waste gasses, such as methane, may become trapped within the internal housing of the pump during operation as a result of maintenance activities when pipes are opened up and repaired or replaced.
This could lead to air binding and prevent the pump from operating properly. It is important to install air vents on the inlet (or suction) side of the pump as well as the outlet (or discharge) side of the pump. You can use manual valves for ease of access.
-
Auto air vents on discharge.
-
Manual air vents connected to suction and discharge pressure gauges.
6. Flow Meter
Once you have purged the air, use a flow meter to confirm flow through the pump. It is common practice to install the flow meter on the discharge side of the pump and send a 4-20mAmp signal back to the VFD, taking advantage of the built in PID loop in the VFD to control flow. Be sure to use the appropriate fittings to connect the flow meter to the pump discharge piping. These fittings should be compatible with the material of construction of the pump and surrounding piping.
7. Pressure Gauges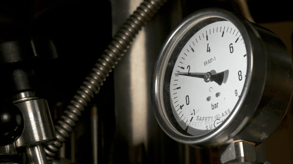
Install pressure gauges on the suction and discharge sides of the pump. Pressure gauges allow you to confirm the pressure across the pump. These pressure gauges can be used to prevent extremely low pressure or vacuum conditions from developing inside the pump. Certain pressure gauges are available in a combination pressure/vacuum style that can detect both pressure and vacuum in one device. You don’t need a pressure switch when installing Discflo pumps, as you would for other types of pumps. Discflo pumps are capable of continuing to run even when the discharge is blocked or deadheaded. In this way, Discflo pumps prevent catastrophic damage under extreme operating conditions, unlike other types of pump designs.
8. Seal Flush
Finally, you need to set up the flush water or barrier water system for the mechanical seal on the pump. Ensure that the process piping used to carry the external process water or other approved lubricants to the mechanical seal is secure. Without the seal flush, you run the risk of damaging the pump’s mechanical seal which will impact pump operations.
Optimizing Your Pump Installation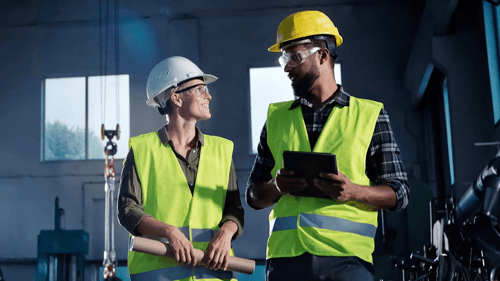
While these tips are an excellent start to ensure a successful pump installation and start up, the best way to optimize your installation and get your operation up and running with minimal downtime is working with a professional team to actually complete the installation.
An installation team is made up of pros for the pump they are installing. While you can use the tips above as a guide on what you’ll need to generally do to prepare for an installation, your installation team should provide you with customized guidance for your unique application, situation, pump, and operation.
Here at Discflo, our experts have installed thousands of pumps with successful start-ups. With minimal downtime, our Discflo disc pumps went to work in the toughest applications, where abrasion, viscosity, entrained air, excessive wear, and corrosion problems wreaked havoc on the prior pumps. Our disc pumps dramatically reduce pump wear, are virtually clog-free, and prevent product damage. As a bonus, our team of experts is always ready to help you handle regular maintenance.
So let our team help you through the installation process, as well. Contact us below to identify the right Discflo pump for you.